Professionals in
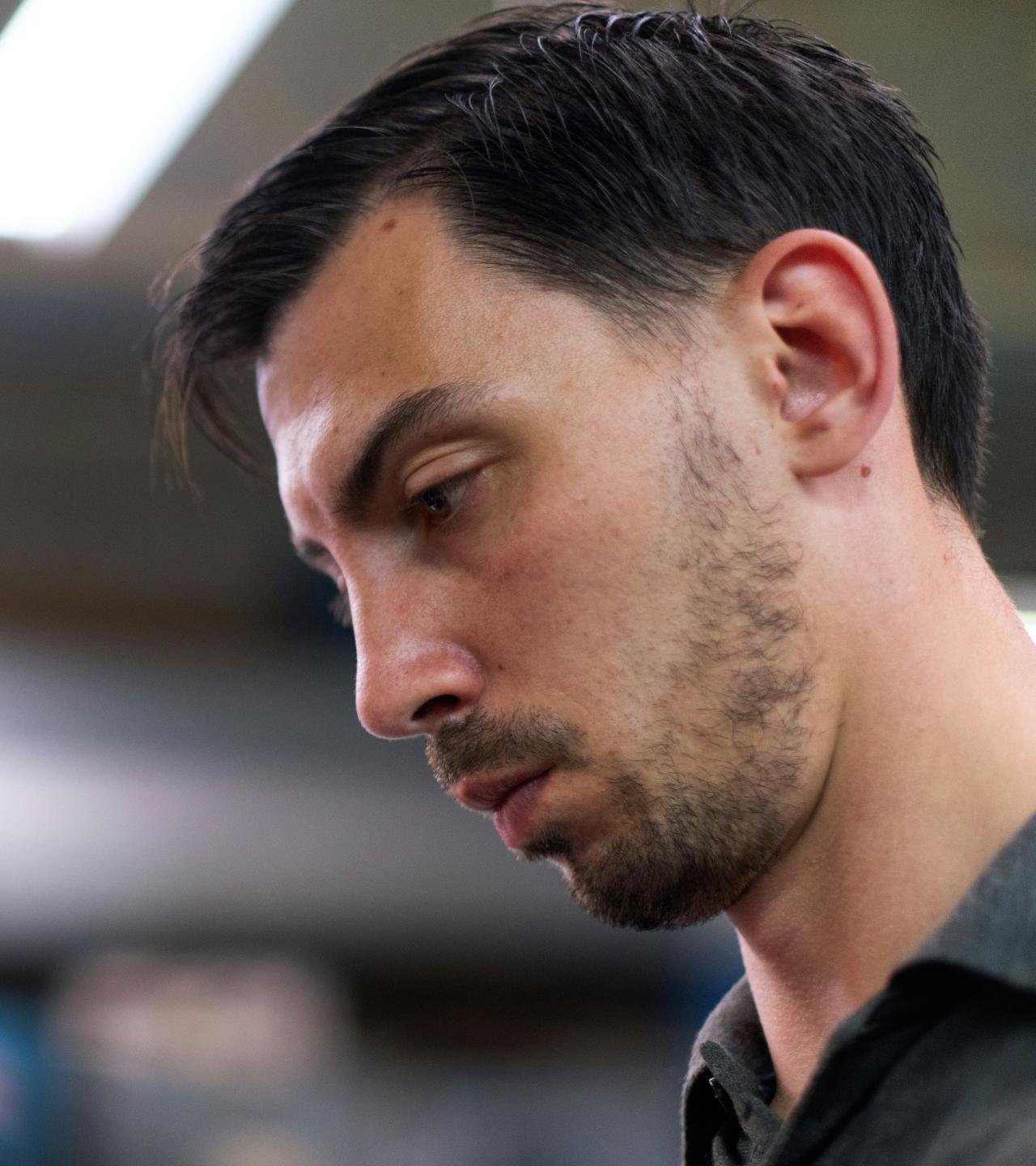
New vacancies
New vacancies
New
Scaffolding Supervisor / Coordinator
Industry
(B) Antwerpen
Project
New
Team Lead OHSE & Ergonomie
Maritime
(NL) Zeeland
Intentional permanent contract
New
Tactical Project Buyer (junior)
Maritime
(NL) Zeeland
Intentional permanent contract
Construction QC Inspector - Civil & Steel Structure
Industry
(B) Antwerpen
Project
Do you have any questions or would you like more information?
Do you have any questions or would you like more information?
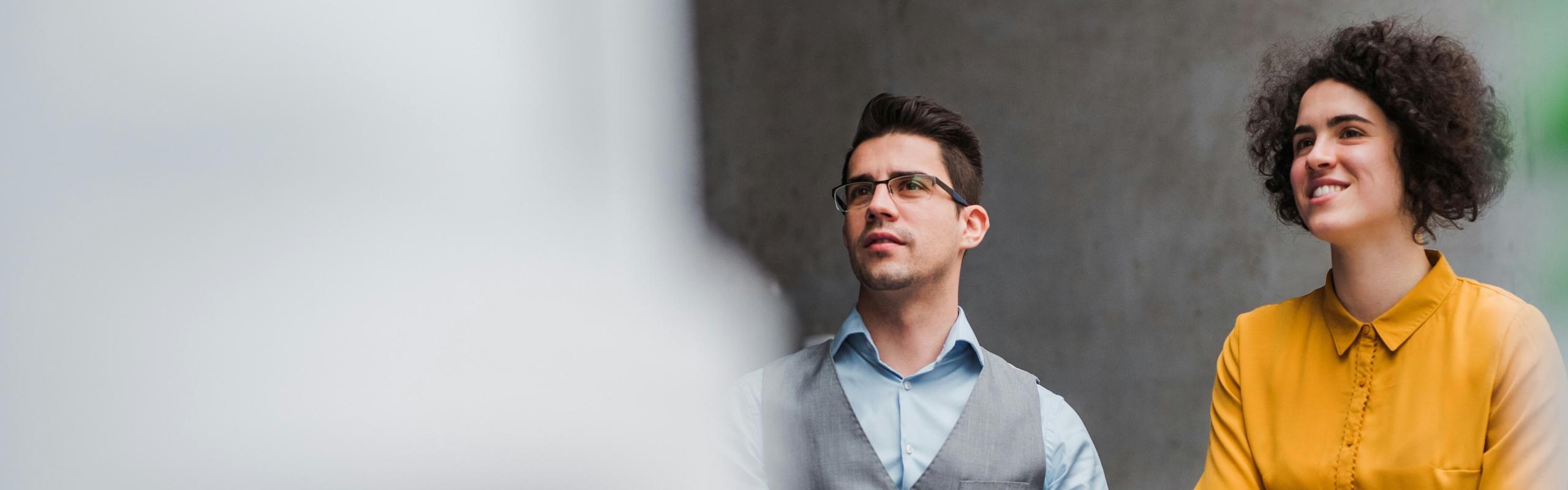